BISON industrial plunger pumps
BISON provides the most suitable industrial high pressure water pumps and triplex plunger pumps according to the specific requirements of flow rate and pressure. It has a wide range of applications, including high-pressure cleaning, cleaning, industrial cleaning, water spraying, water jetting, hydraulic testing, wet sandblasting, splitting, sewer cleaning, transfer, reverse osmosis, descaling, deburring, atomization, injection, and metering. The products provided by BISON are very reliable, efficient, reliable, easy to maintain, and provide long life.
If you need more information about high-pressure pumps for industrial applications and their spare parts, please contact us immediately. We will be happy to provide all the necessary information about our products and also provide you with a detailed quotation.
350Bar 5000PSI industrial high pressure plunger pump
Model | Flow rate | Working pressure | Power | RPM | Inlet size | Outlet size | weight | |||
LPM | GPM | BAR | PSI | HP | KW | RPM | Thread | Thread | KG | |
IP1835 | 18 | 4.7 | 350 | 5075 | 16.9 | 12.6 | 1450 | G3/4″ | G3/8″ | 16 |
IP2135 | 21 | 5.5 | 350 | 5075 | 19.7 | 14.7 | 1450 | G3/4″ | G3/8″ | 16 |
High flow rate 40-74LPM industrial plunger pump
Model | Flow rate | Working pressure | power | RPM | Inlet size | Outlet size | Weight | |||
LPM | GPM | BAR | PSI | HP | KW | RPM | Thread | Thread | KG | |
IP4020 | 40 | 10.6 | 200 | 2900 | 21.5 | 16 | 1450 | G1″ | G1/2″ | 19.8 |
IP5215 | 52 | 13.7 | 150 | 2175 | 21 | 15.6 | 1450 | G1″ | G1/2″ | 19.8 |
IP5620 | 56 | 14.8 | 200 | 2900 | 30 | 22.4 | 1450 | G1″ | G1/2″ | 19.8 |
IP7410 | 74 | 19.5 | 100 | 1450 | 24.1 | 14.8 | 1450 | G1″ | G1/2″ | 19.8 |
500Bar 7250PSI industrial high pressure plunger pump
Model | Flow rate | Working pressure | Power | RPM | Inlet size | Outlet size | Weight | |||
LPM | GPM | BAR | PSI | HP | KW | RPM | Thread | Thread | KG | |
IP1650 | 16.5 | 4.4 | 500 | 7250 | 21.5 | 16 | 1450 | G1/2″ | G3/8″ | 21.6 |
IP2250 | 22 | 5.8 | 500 | 7250 | 29.5 | 22 | 1450 | G1/2″ | G3/8″ | 21.6 |
52HP industrial reciprocating high pressure plunger pump
Model | Flow rate | Working pressure | Power | RPM | Inlet size | Outlet size | Weight | |||
LPM | GPM | BAR | PSI | HP | KW | RPM | Thread | Thread | KG | |
GF3650 | 137 | 36 | 140 | 2030 | 50 | 37 | 900 | G1/2″ | G1″ | 70 |
36HP industrial reciprocating high pressure plunger pump
Model | Flow rate | Working pressure | Power | RPM | Inlet size | Outlet size | Weight | |||
LPM | GPM | BAR | PSI | HP | KW | RPM | Thread | Thread | KG | |
GT4026 | 142 | 38 | 100 | 1450 | 36 | 27 | 1450 | G1/4″ | G1″ | 45 |
30HP industrial reciprocating high pressure plunger pump
Model | Flow rate | Working pressure | Power | RPM | Inlet size | Outlet size | Weight | |||
LPM | GPM | BAR | PSI | HP | KW | RPM | Thread | Thread | KG | |
GE2828F | 70 | 18.5 | 150 | 2180 | 30 | 22 | 1450 | G1″ | G3/4″ | 19 |
350Bar 21LPM industrial reciprocating high pressure plunger pump
Model | Flow rate | Working pressure | Power | RPM | Inlet size | Outlet size | Weight | |||
LPM | GPM | BAR | PSI | HP | KW | RPM | Thread | Thread | KG | |
GPW1821 | 21 | 5.5 | 350 | 5100 | 21 | 15 | 1450 | G3/4″ | G3/8″ or M22*.15 | 17 |
industrial high pressure plunger pumps guide
What are high pressure plunger pumps?
The plunger pump is a reciprocating pump. It uses a fixed high-pressure seal and a smooth cylindrical plunger that slides over the seal, which makes it different in construction from a piston pump. Compared to piston pumps, piston pumps are capable of generating higher pressures and have a wide range of applications in high pressure applications. Plunger pumps are also known as high viscosity pumps, high pressure pumps, or positive displacement pumps because they are able to provide higher pumping pressure than other pump types. In addition, piston pumps can also pump solid and viscous media, so it is widely used in pumping industrial and municipal wastewater.
How does a high pressure plunger pump work?
Both piston and plunger pumps are a type of reciprocating pump. They draw and compress liquids through expanding and contracting chambers. Unlike rotary pumps, the expansion and contraction of the chamber in these pumps is due to the reciprocating motion of the piston or plunger (up, down, and back and forth), rather than a circular (rotating) motion. Piston and plunger pumps have similarities in their operating principles; their main difference is in the way they are sealed. Piston pumps use a reciprocating piston to compress the liquid, and the sealing method is mainly through mechanical gaskets or leather bowl-shaped gaskets; piston pumps use a plunger that slides up and down in the sealing body to compress the liquid, and the sealing method is generally the use of piston rings or seals to achieve. In general, piston pumps and plunger pumps are suitable for different application scenarios. Piston pumps are suitable for relatively low pressure and flow requirements because of their relatively simple sealing structure, while piston pumps are suitable for high-pressure and high-viscosity liquid pumping because they can provide higher pumping pressure and better sealing performance.
Plunger pump function and applications
The plunger pump is a high pressure transfer capability pump, its robust design can efficiently handle a wide range of fluids, including high viscosity substances and heavy materials. As a result, piston pumps are used in a wide range of applications including:
- Injection processes in the chemical field;
- High-pressure homogenization in food and beverage production;
- Industrial and municipal sewage transfer;
- Oil and gas extraction;
- Agricultural irrigation and pesticide application;
- Surface treatment and processing;
- Cleaning treatments and cleaning devices;
- Concrete pumping in construction;
- Pressure testing and other fields.
By using plunger pumps, these applications can operate in a more efficient manner, increasing production efficiency and saving costs.
Among them, industrial plunger pumps come in several types, each designed for specific applications and operational requirements. Below we will take a closer look at three of BISON’s most popular plunger pump types: Industrial high pressure plunger pumps, 40-74lpm industrial plunger pumps, and industrial reciprocating high pressure plunger pumps.
- Industrial high pressure plunger pump: These pumps are primarily used in applications that require a high-pressure fluid transfer, such as in oil extraction, hydraulic pressure testing, and cleaning applications like hydro blasting. They are capable of producing high pressures, often exceeding 20,000 psi.
- 40-74lpm industrial plunger pump: They are suitable for pumping water, chemicals and other liquids during manufacturing and processing. And for transferring fluids in agricultural applications.
- Industrial reciprocating high-pressure plunger pump: These pumps are commonly used in various industries, including food processing, pharmaceuticals, and petrochemicals, where precision dosing and high-pressure capabilities are required.
BISON high pressure plunger pump features
* Pump cylinder: High strength forging(stainless steel, duplex steel, and brass optional)
* Crankcase: Precision die-casting with oxidation blackening surface
* Connecting rod: Forged by aluminum alloy, reinforced by an internal bearing pad
* Plunger: Ceramic tube and surface plasma thermal ceramic thermal spraying
* Seal: Germany original Parkerr brand, high And low-pressure double water seal structure
* Valve: High volume efficiency, spherical sealing structure
* Bearing: Japan’s original NSK brand
* Crankshaft: Made of high strength stainless steel
* Installation direction: Symmetrical left and right
Advantages | Disadvantages |
high pressure plunger pumps have a wide pressure range – can achieve very high pressure | Although rugged and durable, they are less efficient in certain types of viscous or slurry fluids than piston pumps. |
Its structure allows the use of harder materials and ceramic plungers, which are more resistant to wear and corrosion, extending service life and durability. | Their initial cost, running cost, and maintenance cost can be high. |
Plunger pumps can precisely control flow and pressure, allowing operators to adjust parameters according to specific needs and improve process control and productivity. | They may require more precise alignment and settings, which increases the complexity of initial installation. |
There are fewer moving parts in the high-pressure area, and their maintenance procedures are simpler. | high pressure plunger pumps generate a lot of noise and vibration, which requires sound insulation and vibration isolation measures to solve this problem. |
Can handle viscous fluids, slurries and abrasives with proper valve design. | There may be some limitations on the suction capacity of plunger pumps, and proper priming and inlet conditions are required to maintain normal operation and prevent cavitation. |
What factors should be considered when choosing an industrial plunger pump?
Flow requirements:
- Determine the required flow rate in gallons per minute (GPM) or liters per minute (LPM)
- Depending on the application, Consider both average and peak flow demands
- Evaluate whether variable flow control is required for the application
Pressure requirements:
- Identify the maximum operating pressure needed for the system
- Account for any pressure fluctuations or surges that may occur
Fluid characteristics requirements:
- Assess the viscosity, temperature, and chemical composition of the fluid to be pumped
- Determine if the fluid contains abrasive particles or solids
- Consider the fluid’s corrosiveness and compatibility with pump materials
Power requirements:
- Calculate the hydraulic horsepower needed based on flow and pressure requirements
- Factor in the pump’s efficiency to determine the required input power
- Consider available power sources (electric, hydraulic, pneumatic) and their limitations
Environmental requirements:
- Determine the ambient temperature range in which the pump will operate
- Consider humidity levels and potential exposure to moisture
- Evaluate any special environmental factors such as explosive atmospheres or extreme weather conditions
Maintenance and troubleshooting of industrial high pressure plunger pumps
Daily maintenance plan
- Visually inspect seals and connections for leaks and for signs of wear or damage to pump parts.
- Keep the pump area clean to prevent contamination.
- Verify that fluid reservoirs are filled to the proper level and monitor fluid quality, replacing as necessary to avoid contamination.
- Monitor oil levels in gearboxes or bearings, topping off as needed.
- Keep an eye on performance indicators such as flow and pressure readings. If you listen for any unusual sounds, this could indicate a problem.
Importance of Regular Inspections
- Routine checks can identify potential issues before they escalate, preventing costly repairs and downtime.
- Adhering to maintenance schedules ensures compliance with safety regulations, reducing the risk of accidents.
Conclusion
BISON industrial high pressure plunger pumps can play a vital role in various industrial applications and provide superb efficiency and durability. Its sturdy design ensures perfect performance of various demanding tasks. BISON encourages everyone to evaluate their actual needs and make the right choice when choosing a plunger pump.
For dealers who pursue quality and service, BISON is a trusted pressure washer supplier. We not only provide dealers with high-quality plunger pumps but also provide other related pressure washer accessories. Join the BISON family and upgrade your sales experience.
industrial high pressure plunger pump guides written by BISON pressure washer accessories experts
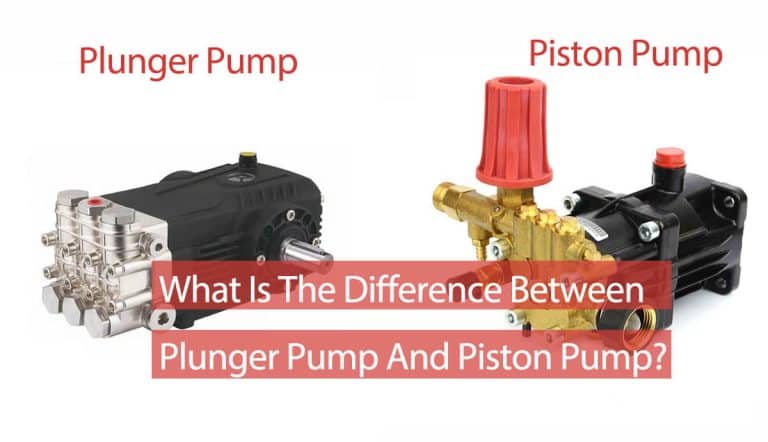
What is the difference between plunger pump and piston pump?
The purpose of this article is to provide a clear comparison of plunger pumps and piston pumps, highlighting their main differences